Design of Experiments (DoE) – Systematic Optimization Method in Plastic Manufacturing
21.03.2025
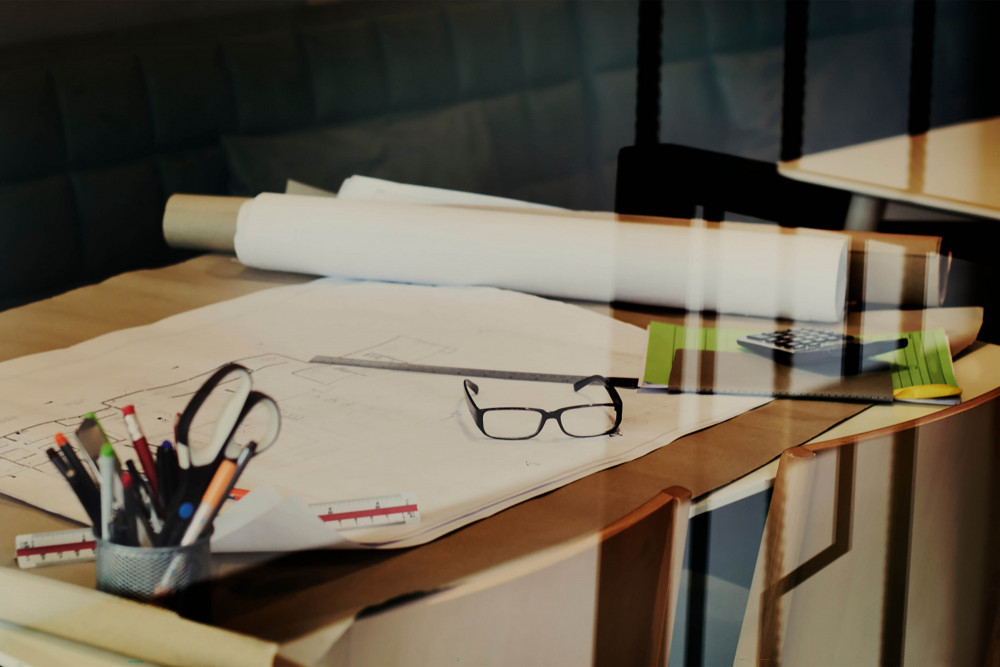
Optimizing products and manufacturing processes is a key competitive factor in the modern plastics industry. One of the most effective methods for this is statistical experimental design, known as Design of Experiments (DoE). This systematic methodology allows us to gain maximum insights with a minimal number of trials, thereby reducing development time, lowering costs, and improving product quality.
At VIAOPTIC, we successfully apply DoE to optimize our optical plastic systems and enhance the robustness of our manufacturing processes. This article explains the fundamentals of this methodology, its application in our production, and the improvements achieved through it.
Fundamentals of the DoE Methodology
Design of Experiments is a scientifically based method for planning, conducting, and analyzing experiments using mathematical and statistical techniques. Unlike traditional trial-and-error approaches, DoE enables a systematic examination of influencing factors and their interactions with target variables. Originally developed in agricultural research, this method has long since been established in the industry—especially in plastics technology, where complex relationships exist between materials, processes, and product properties.
Statistical experimental design plays a crucial role in both our product development and the optimization of production processes. With these methods, we can generate reliable knowledge with as few experiments as possible, which can then be used for product optimization or to enhance process robustness.
Structured Approach in Design of Experiments
The DoE methodology follows a structured approach consisting of several phases. First, relevant influencing and target variables are identified. Influencing variables are the parameters that can be adjusted (such as temperature, pressure, material composition), while target variables represent the product properties to be optimized (such as strength, surface quality, or dimensional accuracy). Different factor levels are then defined, and experimental designs are developed to ensure efficient testing.
Various experimental approaches are used in DoE, including single-factor experiments, full factorial designs, and Taguchi’s orthogonal arrays. The choice of experimental design depends on the complexity of the problem, the number of factors to be examined, and the available resources. Once experiments are conducted, a statistical analysis identifies main effects and interactions. These insights are then used to develop models that describe system behavior and enable predictions.
Unlike the conventional "test to pass" approach, where the focus is solely on verifying whether a product meets predefined requirements, DoE allows for a deeper understanding of system behavior. The "test to failure" approach, which explores system limits, provides valuable information for product optimization and risk minimization. By systematically varying influencing factors, we can quantify the relationships between process parameters and product properties, enabling well-informed decisions and achieving the high precision required for optical applications.
Application of DoE in Plastic Manufacturing
DoE is widely used in the plastics industry, from material development and process optimization to quality assurance. It is particularly beneficial for complex manufacturing processes such as injection molding. The high demands in this field have led to continuous improvements in components, tools, and production methods—an effort that would be highly time- and cost-intensive without systematic methodologies.
DoE in Injection Molding of Plastic Parts
At VIAOPTIC, we utilize DoE primarily to optimize the injection molding process. Numerous factors influence the quality of the final product in injection molding, including melt temperature, injection speed, holding pressure, mold temperature, and cooling time. Using DoE, we can precisely analyze the effects of these factors and their interactions.
By leveraging simulation software, we conduct virtual experiments with different test designs before launching real-world trials. This allows us to identify potential issues and develop solutions early in the development phase. Simulation enables us to explore various scenarios and determine the optimal process parameters without requiring costly tooling modifications or extensive experimental series.
Benefits and Impact of DoE at VIAOPTIC
Implementing DoE in our development and production processes has led to numerous advantages. With a systematic approach, we can shorten development cycles, reduce costs, and improve product quality. The methodology helps us extract maximum insights from a limited number of experimental trials and find optimal solutions for different criteria.
Increased Efficiency and Cost Reduction
One of the primary advantages of DoE is its ability to increase efficiency. Through targeted experiment planning and execution, we can obtain meaningful results with far fewer trials than conventional trial-and-error methods. This results in significant time savings in development and optimization.
Additionally, DoE findings help reduce scrap and rework. By optimizing process parameters and understanding influencing factors, we can ensure consistent product quality and minimize variations—directly impacting production costs.
Quality Improvement and Process Robustness
DoE not only helps us determine optimal process settings but also enhances process robustness. A robust process is less susceptible to disturbances and maintains consistent results even when input variables fluctuate. This is especially critical in plastics manufacturing, where material batches may vary and environmental conditions can affect the process.
By analyzing interactions between different factors, we can identify critical parameters and implement control measures to mitigate their effects.
Conclusion: DoE as a Key to Continuous Improvement
Statistical experimental design (DoE) has become an indispensable tool for product and process optimization at VIAOPTIC. With a systematic approach, we can extract maximum insights with minimal resources and make well-founded decisions.
The benefits of DoE are extensive: shorter development times, lower costs, higher product quality, and more robust processes. In plastics manufacturing, where complex interactions exist between materials, processes, and product properties, this method offers significant advantages. It enables us to meet increasing customer demands and differentiate ourselves in the market.
Successful implementation of DoE requires not only methodological expertise but also the right tools and a corporate culture that embraces data-driven decision-making. Through continuous training and the use of modern software, we have created the foundation to leverage the full potential of this methodology.
Looking ahead, we plan to further expand our use of DoE and integrate it with new technologies. Our goal is to continuously improve our products and processes. In this effort, statistical experimental design is not just a tool but an integral part of our corporate philosophy, which is built on scientific methods and data-driven insights.
Bild: 123rf.com, rawpixel